“These are all common-sense ideas that anybody with half a brain could have figured out years ago. Instead of spending beaucoup bucks on consulting and design, the hospital administrators could have done what they should have done in the first place, and simply asked the nurses for their suggestions.” – Unknown
The best solutions to problems encountered in the daily work can most often be found with the experts involved in actually performing the daily work. We spoke of constraints and standards. Now we need to consider trust for a moment.
How many managers would trust their workforce to design the daily work?
Would you be comfortable in allowing a front line worker to alter a process?
How would you feel about having a component design altered by an assembler?
What if a material handler redesigned how the warehouse was laid out?
Chances are the concept has some fear attached to it for you. To make these kinds of changes, we would typically rely on experts, like; consultants, suppliers or process/design engineers. Truth is they may offer some excellent ideas. To do so though, overlooks the expert resources right there in your own organization. The people, who perform the work every day, probably have some creative insights.
That material handler may prefer to have the fastest moving items close at hand to make picking and stocking faster.
The assembler may have recognised a small change to a component can eliminate the need for an additional fastener, making assembly less complex, reducing the number of parts and speeding the process.
Before the workforce starts changing things, there needs to be some learning, procedures, disciplines and trust.
The workforce will need some tools, standard disciplines to trial changes, communicate results with all affected, obtain test results, analyse the effectiveness and impact of the proposed change; all before implementation. In this way the downstream customers will know that care has been taken to ensure any change implemented has been well thought out.
Management doesn’t really need to do the thinking for everyone. Think of the weight off your shoulders if the entire workforce has a shoulder to the wheel and is working daily to create and deliver the highest possible customer value through relentless innovation.
Want to learn more about fully engaging your entire workforce?
Email me leanthoughtstarter@gmail.com
Tweet
About Me
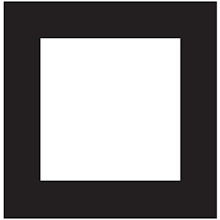
- Lean Thought Starter
- C-Level executive passionate about the application of innovation at all levels of an organization in support of the continual pursuit of perfection. Learn more at www.wspsolutions.ca
2010-12-31
Want ideas? –Ask your workforce!
Labels:
boss,
constraints,
continual improvement,
Deming,
Ford,
hospital,
idea,
innovation,
investigation,
job,
kaizen,
kata,
lean,
nurse,
problem,
solution,
standard,
Waste,
work
2010-12-23
Standards – are they the foundation for kaizen and employee engagement?
“Today’s standardization…is the necessary foundation on which tomorrow’s improvement will be based. If you think of “standardization” as the best you know today, but which is to be improved tomorrow-you get somewhere. But if you think of standards as confining, then progress stops.” – Henry Ford
We looked at how constraints defined the sand box you play in; now let’s examine the role standards play in the daily work. Way back in 1926 when Henry Ford was writing about standardization in his book, Today and Tomorrow, he was pointing out that to improve a process you need to have a repeatable process to begin with. We refer to this as a standard. The standard identifies the sequence and timing of the work, as well as the tools and components necessary for the defined outcome. You know everyone who follows the standard will arrive with the same result. The standard is a training aid and reference guide. Many think the standard is restricting in that it restricts creativity. No doubt the standard is controlling, however it is the foundation for change in this way:
Create a standard
Follow the standard
Improve the standard
Repeat endlessly
This is Kaizen, continual improvement.
Who best creates the standard? The people who perform the task
Who best follows the standard? The people who perform the task
Who best improves the standard? The people who perform the task
When the front line workers are actively engaged in improving the standards of the daily work amazing events will begin to occur. Many, many small improvements at the front line of the work will elevate how your organization creates and provides customer value to the highest possible level.
To facilitate this, some learning will need to take place and some trust will need to be provided.
Would you like to see this level of engagement at your workplace?
To discuss or learn more Email me at www.leanthoughtstarter@gmail.com
Tweet
We looked at how constraints defined the sand box you play in; now let’s examine the role standards play in the daily work. Way back in 1926 when Henry Ford was writing about standardization in his book, Today and Tomorrow, he was pointing out that to improve a process you need to have a repeatable process to begin with. We refer to this as a standard. The standard identifies the sequence and timing of the work, as well as the tools and components necessary for the defined outcome. You know everyone who follows the standard will arrive with the same result. The standard is a training aid and reference guide. Many think the standard is restricting in that it restricts creativity. No doubt the standard is controlling, however it is the foundation for change in this way:
Create a standard
Follow the standard
Improve the standard
Repeat endlessly
This is Kaizen, continual improvement.
Who best creates the standard? The people who perform the task
Who best follows the standard? The people who perform the task
Who best improves the standard? The people who perform the task
When the front line workers are actively engaged in improving the standards of the daily work amazing events will begin to occur. Many, many small improvements at the front line of the work will elevate how your organization creates and provides customer value to the highest possible level.
To facilitate this, some learning will need to take place and some trust will need to be provided.
Would you like to see this level of engagement at your workplace?
To discuss or learn more Email me at www.leanthoughtstarter@gmail.com
Tweet
2010-12-16
Constraints, are they helping you innovate?
‘Art consists of limitation. The most beautiful part of every picture is the frame.” - Gilbert Keith Chesterton
Your job has specific areas of responsibility. These will define where your work begins and where it ends. Inputs are provided and outputs are produced. Your outputs are for an internal or external customer. In some cases you may provide outputs for both internal and external customers.
This is your sand box. In this framework of limits is where you will look for problems that need solutions.
But where do you start?
Start with the problems that affect the daily work. What wastes can you identify and eliminate. Do you want to look for things that can be done better? No. You want to create a vision of perfection and then remove those problems one by one that prevent your vision of perfection being reality. Consult with your internal and external customers; they should have no problem telling you what problems they see inside your constraints that are impacting them.
You may have heard it said that necessity is the mother of invention. In your world the constraints you must deal with will motivate a higher level of problem solving. The goal is to find no cost, low cost solutions to your everyday work problems. It is unlikely you will get any support or resources to make the changes you see are required. This will help kick your innovation abilities to a new level.
The more defined this frame of constraints is, the better.
Tweet
2010-12-06
What role does innovation play in your job?
For many of us, innovation is just not on the daily agenda. First there are all those important meetings that you must attend. This is followed by priority interruptions. Then the unexpected, but consistently appearing, emergency fire fighting. By now the day is shot and you are staying late to review correspondence, read reports, write reports and prepare for tomorrows important meetings.
What would happen if you went to the boss and asked if you could block out a portion of your day to work on improvements for your daily work? Let me know how this works out for you.
Now you have a block of time to begin the review of your own daily work or not. If you do, ask:
What do you do all day?
Why are these things necessary to do?
Why is that?
Why is that?
Why is that?
Why is that?
Who are your customers?
What problems do the jobs you perform solve for your customers?
You may have questions of your own, please include them. As you gather answers you are investigating your job. The activities that you do daily as part of the routine are now being questioned. You are breaking out of your complacency and looking at what has become routine over time with fresh eyes.
With all of this investigation, problems will begin to appear. Choose a problem that affects the daily work and document it as clearly as possible. If others perform the same job as you, review what you see as the problem with them. Ask them to help clarify the problem with you. Ask your boss if the problem has been clearly defined and understood. You may choose to include your customer in the conversation if the problem impacts the outputs you pass on to them.
Why start with what you do? Typically you have the highest level of knowledge and insight into the work. After all you are performing the job. Making changes to your own work by applying creative ideas will provide the experience of innovating. Implementing many small innovations that impact the daily work will form the basis of a discipline of continual improvement. You will learn how to apply the tools we will talk about in future blogs through firsthand experience. Your confidence will be bolstered by your own successes. Hopefully your boss will also recognize the effort and improvements you have implemented.
Now you can begin to visualize the ideal solution to that problem you have selected to resolve.
Ask yourself; what would perfection look like?
Please comment on this blog, you can also email me; leanthoughtstarter@gmail.com
Tweet
2010-11-29
Welcome to the Lean Thought Starter
Is continual improvement the place to start your lean journey?
Many people feel the implementation of a continual improvement initiative, with the promise of low hanging fruit payoffs, is the first step on the path to becoming lean. Continual improvement is required by many as evidence that the organization is moving forward in the pursuit of perfection. Yet all too often continual improvement gets confused as a tool for quality problem solving or kaizen blitzes. Management begins to lose interest as the low lying fruit is gathered and initiates a search for the next silver bullet.
Many fail to realize continual improvement is a required discipline, to be applied everyday by everyone as a tool in the pursuit of perfection. Making perfection the goal, opens the door to creative thinking and innovation at all levels of the organization.

Over the coming weeks I will explore this topic in much more detail. I look forward to having you participate in the journey.
Until then, ask yourself this; what role does innovation play in your job?
You can also email me; leanthoughtstarter@gmail.com
Subscribe to:
Posts (Atom)